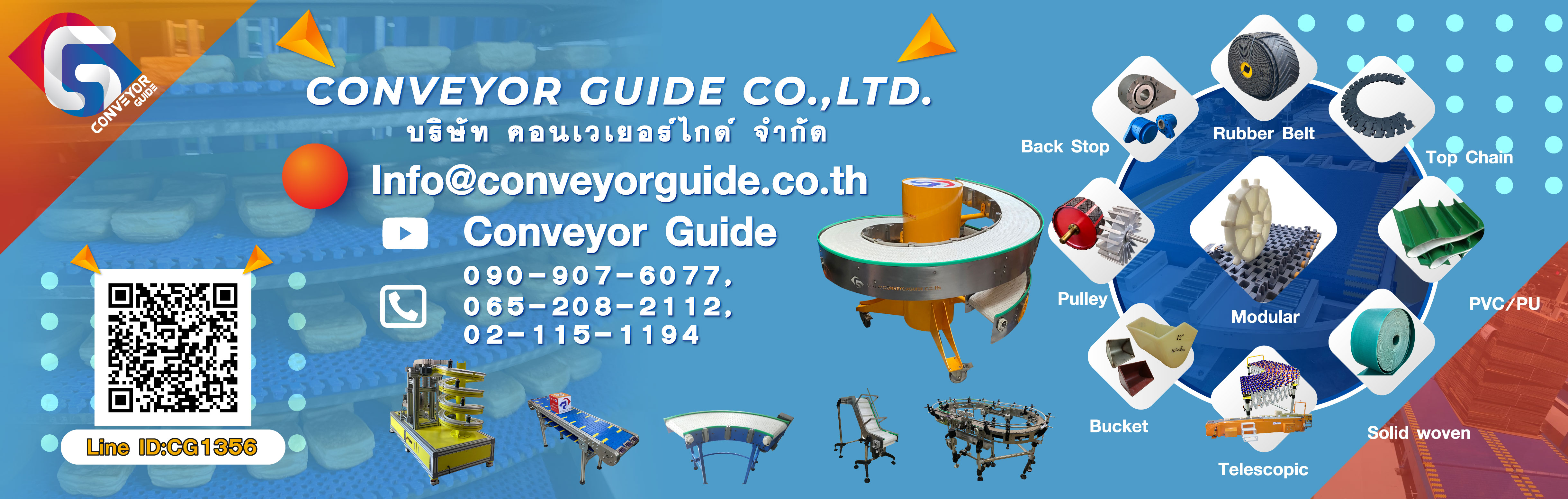
>> 7.2 General conveyor Guide Design (คำแนะนำ: แนวทางทั่วไปการออกแบบระบบสายพานโมดูล่าร์)
1. General Design Guide: Modular Belt Conveyor System
คำแนะนำ: แนวทางทั่วไปการออกแบบระบบสายพานโมดูล่าร์ 1.ความเป็นมา เนื่องจากสายพาน Modularเป็นผลิตภัณฑ์ที่เกิดขึ้นมาแค่ 40 ปี จึงจัดว่ายังเป็นเรื่องใหม่ในวงการสายพานเมื่อเปรียบเทียบกับสายพานประเภทอื่นๆ (สายพานยางดำมากกว่า 100 ปี สายพาน Top Chain 96 ปี) จากการที่ Conveyor Guide ออกตลาดเยี่ยมลูกค้าเพื่อแนะนำผลิตภัณฑ์สายพานโมดูล่าร์และสอบถามเกี่ยวกับปัญหาและความต้องการอื่นๆที่ลูกค้าต้องการ พบว่าลูกค้าหลายรายต้องการสร้าง Modular Belt Conveyor เอง เพื่อประหยัดเงิน และสามารถพึ่งพาตัวเองได้ในการซ่อมแซมและบำรุงรักษา เรายังพบความจริงอีกว่าส่วนมากแล้วเมกเกอร์ (Maker) ในฐานะมือสร้างเครื่องจักรอาชีพก็จะสามารถสร้าง Modular Belt Conveyor กันเองได้โดยอัตโนมัติ เพียงแค่สอบถามเพื่อทราบความต้องการและลักษณะการทำงานของ Conveyor แล้วก็สามารถจินตนาการได้เลยว่าจะสร้าง Conveyor ขึ้นอย่างไร หรือถ้ามีผู้ที่เคยทำมามีตัวอย่างอยู่ก่อนแล้ว ก็ถือโอกาสตาม copy สิ่งที่เคยทำกันมา ของเดิมเป็นยังไงของใหม่ก็ทำตามนั้น โดยไม่ได้คำนวณหรือคำนึงถึงหลักการทำงานที่ดีหรือถูกต้องเป็นอย่างไร ถ้าของเก่าทำมาดี สิ่งแวดล้อมที่ใช้งานเหมือนกับของใหม่ที่ Copy มาก็จะรอดตัวไปด้วย เมื่อเราสอบถามเรื่องการกำหนดระยะต่างๆของโครงสร้างและการเลือกมอเตอร์ได้มีการคำนวณหรือไม่ เมกเกอร์(Maker) ส่วนมากก็จะตอบว่าไม่เคยมีการคำนวณเลยใส่ขนาดของมอเตอร์ไปเลยโดยประสบการณ์ก็สามารถทำงานได้ แต่จะดีผิดหรือถูกหรือมีประสิทธิภาพหรือไม่ก็ไม่ได้มีการประเมินเช่นกัน เราถามต่อไปว่าทำไมถึงไม่คำนวณมันยากหรือมันเสียเวลามากน้อยยังไง คำตอบที่ได้ ส่วนมากคือไม่มีเวลาทำและหาตำราหรือความรู้มาอ้างอิงยากลำบากเพราะตำราที่เขียนเป็นภาษาไทยก็ไม่มีใครนำมาเผยแพร่ สรุปคือ “ผู้สร้างเครื่องจักรขาดข้อมูลหรือหาข้อมูลไม่ได้” วันนี้ Conveyor Guide ขออาสานำเรื่องความรู้ดีๆของ Modular Belt Conveyor มาแชร์แบ่งปันกัน เนื่องจากเราตระหนักว่าวิธีทำงานที่มีหลักการเป็นเหตุเป็นผล เช่น การวาง layout การเลือกขนาดของมอเตอร์และการคำนึงถึงสิ่งแวดล้อมต่างๆที่สายพานทำงานมีความสำคัญมาก Conveyor Guide ได้รับความรู้ดีๆจากการศึกษาคู่มือของผู้ผลิตสายพานหลายๆรายจึงนำมาแชร์แบ่งปันกัน ให้ผู้ที่มีส่วนได้เสียอยู่ในวงการได้มีการพัฒนางานในทุกระดับ ต้องขอขอบคุณและขออนุโมทนาต่อผู้ผลิตสายพานทุกค่ายที่ผู้เรียบเรียงมิได้เอ่ยนาม แต่ได้นำความรู้ที่เป็นประโยชน์มาเผยแพร่ให้ผู้สนใจได้ศึกษาไว้ ณ.ที่นี้ด้วย
2.วัตถุประสงค์ วัตถุประสงค์ของบทความชิ้นนี้ก็คือ 1 ช่วยให้ผู้ที่เกี่ยวข้องโดยเฉพาะผู้สร้างเครื่องจักร (Maker) สามารถวาง Layout และ คำนวณหาค่าแรงต่างๆ เลือกขนาดของมอเตอร์ได้ด้วยความมั่นใจและมีหลักการ 2 ช่วยให้ ผู้เกี่ยวข้องรวมทั้ง End User สามารถตรวจสอบรูปแบบเบื้องต้นของ Conveyor การวาง Lay out โครงสร้างของสายพานดูล่าร์ที่ถูกต้องซึ่งถ้าออกแบบที่ถูกต้องแล้วอายุการทำงานของ Conveyor จะยาวนาน เข้าใจหลักการทำงานซึ่งจะนำมาซึ่งการบำรุงรักษาที่ถูกต้องเป็นการประหยัดเงิน ประหยัดพลังงานของตนเองประเทศชาติและโดยส่วนรวม 3 ส่งเสริมให้ผู้เกี่ยวข้องในวงการมีหลักการ มีความรู้ในการสนับสนุนความมั่นใจในทำงาน เป็นการพัฒนาบุคลากรในวงการขนถ่ายลำเลียง Scope ของบทความจะประกอบด้วย Ø 1.General Designed Guide(คำแนะนำทั่วไปการออกแบบ) Ø 2.Horizontal Conveyor Designed Guide(การออกแบบสายพานวิ่งในแนวราบ) Ø 3.Inclined Conveyor Designed Guide(การออกแบบสายพานวิ่งในแนวเอียง) Ø 4.Curve Conveyor Designed Guide(การออกแบบสายพานวิ่งโค้ง) o Flush Grid Curve(สายพานโค้งแบบธรรมดา) o Special Curve(สายพานโค้งแบบพิเศษ) Ø 5.Spiral Conveyor Design Guide(การออกแบบสายพานแบบบันไดเวียน) Ø 6.Sprocket Arrangement Guide(คำแนะนำการติดตั้งเฟืองขับ) Ø 7.Product Transfer Designed Guide (คำแนะนำการออกแบบจุดเชื่อมต่อ) Ø และเรื่องอื่นๆเพิ่มเติม...ถ้าผู้เขียนยังมีเรี่ยวแรงเหลือพอ
Typical โครงสร้างของ Modular Belt Conveyor แนวตรงในแนวราบแบบง่ายๆ
Typical โครงสร้างของ Modular Belt Conveyor แนวโค้งในแนวราบแบบง่ายๆ
3. Conveyor Belt, Sprocket and Related Data (ความสัมพันธ์ของข้อมูลระหว่างอุปกรณ์ต่างๆในระบบ สายพานโมดูล่าร์) ก่อนอื่นผู้เขียนขอทำความเข้าใจก่อนว่า ตัวอย่างที่นำเสนอนี้ได้นำมาจาก Catalog ข้อมูลของผู้ผลิตหลายยี่ห้อปะปนกัน เนื่องจากแต่ละค่ายก็จะมีข้อมูลดีๆไม่เหมือนกัน ผู้เขียนจึงได้รวบรวมสิ่งที่คิดว่าเป็นประโยชน์จากหลายๆแหล่งมาจัดไว้ในที่เดียวกัน ซึ่งผู้อ่านจะไม่เสียเวลาในการค้นคว้าและได้ประโยชน์อย่างครบถ้วน ผู้เขียนมีจุดประสงค์เพียงเพื่อให้ท่านผู้อ่านมีความรู้ เห็นภาพและเข้าใจในหลักการทำงานและหน้าที่ของอุปกรณ์ต่างๆของระบบสายพาน Modular เท่านั้น ไม่มีเจตนาจะเชียร์สินค้าตัวหนึ่งตัวใดหรือของยี่ห้อใดเป็นการเฉพาะ ตัวย่อและคำจำกัดความจะแตกต่างกันไปในแต่ละยี่ห้อแต่หลักการทำงานไม่ได้แตกต่างกันจนมีนัยยะสำคัญ ขอให้ผู้อ่านค่อยๆพิจารณาเอาเอง สำหรับข้อมูลที่จะใช้ทำงานออกแบบหรือผลิตจริง ไม่ว่าท่านจะซื้อสายพานจากตัวแทนจำหน่ายยี่ห้ออะไรก็ตาม ข้อมูลเหล่านี้(เช่น คำย่อ ระยะและรูปร่างของ Layout) สามารถขอได้กับผู้ขายที่ท่านสั่งซื้อสายพานยี่ห้อนั้นๆได้โดยตรง หน้าผู้เขียนต้องการอธิบายให้ท่านเข้าใจหลักการแบบง่ายๆว่าแต่ละส่วนมันมีหน้าที่อะไร ทำงานร่วมกันได้อย่างไร ถ้าเข้าใจเรื่องพื้นฐานเหล่านี้ของผู้ผลิตรายใดรายหนึ่ง ก็จะเข้าใจเรื่องคล้ายกันของผู้ผลิตสายพาน ยี่ห้อใดๆก็ได้ตามไปด้วย ผู้เขียนจะเสนอข้อมูลที่เป็นข้อเท็จจริงให้ท่านเข้าใจ ผู้เขียนเชื่อว่าผู้อ่านฉลาดทุกท่าน ดังนั้นผู้อ่านจึงมีอิสระในการพิจารณาเลือกซื้อสินค้ากับใคร ยี่ห้อใดก็ได้ที่ให้ความคุ้มค่าโดยรวมแก่ท่านสูงสุด ข้อมูลที่นำเสนอต่อไปนี้เป็นสายพานลำเลียงแนวตรงแบบง่ายๆที่นิยมใช้กันมากที่สุด ซึ่งเป็นข้อมูลที่ใช้ได้เป็นการทั่วไป หากการออกแบบ ส่วน Conveyor ที่สลับซับซ้อนผู้อ่านต้องศึกษาและปรับการออกแบบให้เหมาะสมกับการใช้งานในสิ่งแวดล้อมที่เปลี่ยนไปต่อไปหรือสอบถามเราหากมีอะไรที่ยังไม่เข้าใจ
Layout แบบง่ายๆของระบบสายพานโมดูล่าร์
คำย่อต่างๆมีความหมายดังนี้ M คือ (Driving Shaft) หรือ เพลาขับ เป็นได้ทั้งหน้าตัดรูปสี่เหลี่ยม(Square) หรือรูปกลม(Round) ข้อแตกต่างกันคือ เพลาขับหน้าตัดรูปสี่เหลี่ยม(ไม่มีลิ่ม-Keyway) มีข้อได้เปรียบเพลาขับหน้าตัดรูปกลม(มีลิ่ม-ส่งผ่านแรงบิดโดยลิ่ม- Keyway) คือเมื่อที่มีการเปลี่ยนแปลงอุณหภูมิ(เพิ่มหรือลด)ในขณะที่ conveyor ทำงาน เพลาขับรูปสี่เหลี่ยม(Square ปรกติเป็นเหล็ก) สามารถส่งแรงบิดผ่านเพลาโดยตรงมายัง Sprocket (ปรกติจะเป็นเฟืองพลาสติก)ทุกตัว (โดยไม่ต้องมีลิ่มและร่องลิ่ม) อีกทั้ง sprocket สามารถยืดหยุ่นปรับตัวและสามารถเคลื่อนที่(ตามความยาวของเพลา) ได้อิสระอย่างง่ายบนเพลาขับรูปสี่เหลี่ยม Ø ประสิทธิภาพเพลาขับ หน้าตัดรูปสี่เหลี่ยม(Square) สามารถส่งผ่านแรงบิด(Torque) ได้สูงกว่าเพลาหน้าตัดรูปกลมกลมเนื่องจาก เพลาขับรูปสี่เหลี่ยม(Square) สัมผัสกับเส้นรอบรูปภายในรูของ Sprocket อย่างเต็มหน้าตัด ขณะที่เพลาขับกลม(Round) จะมีเฉพาะส่วนพื้นที่ของ keyway เล็กน้อยเท่านั้นสัมผัส ดังนั้นการส่งส่งผ่านแรงบิด(Torque) จึงทำได้น้อยและเกิดความเค้น (Stress) สูง ณ.จุดสัมผัส ทำให้อายุการใช้งานต่ำ Ø ในทางปฏิบัติ การติดตั้งเฟือง (Sprocket) กับเพลาขับจะทำโดยจะล็อก (Fix) Sprocket ตัวกลางไว้กับเพลาขับ เพื่อบังคับให้สายพานวิ่งได้ตรงแนว (Good Tracking) ส่วนเฟือง(Sprocket) ที่เหลือปล่อยให้เคลื่อนที่ในแนวราบด้านข้างได้อย่างอิสระบนแกนของเพลา(จะมีรายละเอียดในบทความอื่นอีกต่างหาก) เพื่อรองรับการยืด-หดตัวของ Sprocket และเพลาเนื่องจากการเปลี่ยนแปลงอุณหภูมิ U (Idling Shaft) คือเพลาตัวตามติดตั้งที่อีกปลายด้านหนึ่งของ conveyor สามารถเป็นได้ทั้ง เฟือง (sprocket) ลูกกลิ้งเหล็ก (Steel Roller) หรือลูกกลิ้งพลาสติกก็ได้ ST คือส่วนรองรับน้ำหนักบรรทุกด้านบน (Carry Way) ซึ่งสามารถใช้ wear stripวางตามแนวขนานระหว่างส่วนหัวและส่วนท้ายหรือวางเป็นก้างปลา (V Shape) ของ Conveyor ก็ได้ wear strip จะเป็นตัวช่วยลดแรงเสียดทานระหว่างสายพานและโครงสร้างของ conveyor
Wear Strip แบบวางขนาน (ทำง่าย ราคาถูกเหมาะสำหรับงานเบา)
Wear Strip แบบก้างปลา (V Shapeเหมาะสำหรับงานหนัก การสึกหรอของสายพานจะสม่ำเสมอ สามารถทำความสะอาดที่ท้องสายพานได้ดี)
SR คือส่วนรองรับน้ำหนักบรรทุกด้านล่าง (Return) ของสายพาน สามารถใช้ลูกกลิ้งหรือวาง wear strip ตามแนวขนาน ก็ได้ CA (Catenary Sag) เรียกแบบไม่เป็นทางการว่า “ระยะตกท้องช้าง” เป็นระยะที่ปล่อยไว้เป็นอิสระมีหน้าที่ Ø เก็บความยาวของสายพานส่วนเกิน จากการขยายตัวหรือหดตัวของอุณหภูมิหรือจากน้ำหนักของวัสดุบรรทุกที่ทำให้ความยาวของสายพานเปลี่ยนไปหรือจากความยาวที่เพิ่มขึ้นจากการสึกหรอ(ยืดตัว) ของ Joint สายพาน Ø แรงดึง(น้ำหนัก) จากสายพานด้านหย่อนจะทำหน้าที่ปรับระยะให้สายพานตึงพอเหมาะที่จะทำให้สายพานและเฟือง (Sprocket) ทำงานร่วมกันได้อย่างมีประสิทธิภาพ สายพานวิ่งได้อย่างราบเรียบไม่กระโดดหรือไม่ Slip TU (Take Up) คืออุปกรณ์ปรับตึงที่ใช้ปรับระยะตกท้องช้างให้มีระยะพอเหมาะกับการทำงานของ Sprocket กับสายพาน อุปกรณ์นี้อาจจะเป็นใช้แบบ Screw หรือเป็นแบบตุ้มถ่วง (Gravity Take Up) หรือเป็นระบบนิวเมติกก็ได้ Fe (Effective Tension) คือแรงดึงสุทธิหรือ Belt Pull เป็นแรงดึง ณ.ตำแหน่งก่อนเข้า Drive Sprocket ใน Conveyor แบบธรรมดา (Simple Conveyor) เกือบทุกกรณีแรงดึงของสายพาน ณ.ตำแหน่งนี้จะมีค่าสูงสุด (maximum) ทั้งนี้แรงดึงสูงสุดยังขึ้นอยู่กับแรงเสียดทานระหว่างสายพานและที่รองรับ support ต่างๆ (ST/SR) รวมทั้งผลกระทบที่เกิดการสะสม (Accumulation) ของวัสดุที่ลำเลียง (โหลด) ด้วย แรงดึงสูงสุดใช้ในการเลือกค่าแรงดึงเพื่อเลือก Series ของสายพาน V (Belt Speed) ปกติแล้วสายพาน Modular ไม่ควรใช้ความเร็วของสายพานเกิน 50 เมตรต่อนาที (หรือ 150 ฟุตต่อนาที) ถ้าความเร็วมากขึ้นอายุการใช้งานของสายพานจะสั้น และจะเกิดการกระดก/กระตุก/กระโดด เพราะสายพานขบกับ Drive Sprocket ไม่ดี ปรากฏการณ์นี้เรียกว่าเรียกว่า Polygon Effect หรือ Chordal Action ซึ่งผลกระทบจะมากน้อยแค่ไหนขึ้นอยู่กับจำนวนฟันของ Sprocket ยิ่ง Sprocket มีฟันมากความแตกต่างของความเร็วสายพานก็จะเปลี่ยนแปลงน้อย (วิ่งได้เรียบ)
MP (Product Weight) คือน้ำหนักบรรทุกหรือโหลดที่ conveyor ต้องลำเลียงในการคำนวณใช้สมมุติฐานว่าน้ำหนักบรรทุกจะกระจายไปทั่วพื้นผิวของสายพานเท่าๆกัน โดยมีค่าเป็น น้ำหนักต่อตารางเมตรหรือตารางฟุต เช่น 10 กิโกกรัมต่อตารางเมตรเป็นต้น MB (Belt Mass) คือน้ำหนักของตัวสายพานเอง เป็นตัวใช้คำนวณแรงเสียดทานระหว่างสายพานและ wear strip ที่รองรับ
4.ขอนำเสนอข้อมูลอีกชุดหนึ่งชุดซึ่งให้รายละเอียดในบางหัวข้อนอกเหนือจากที่นำเสนอในข้างต้นได้ดี
Layout แบบง่ายๆของระบบสายพานโมดูล่าร์
Layout แสดงระยะที่สำคัญในการออกแบบระบบสายพานโมดูล่าร์
เมื่อ Rod (Hinge) อยู่ในต่ำแหน่งสูงสุดของ Sprocket สายพานจะยกตัวสูงกว่าแนวระดับ เมื่อ rod เคลื่อนที่ผ่านจุดสูงสุดแล้ว สายพานก็จะกลับสู่แนวระดับอีกครั้งหนึ่ง
ระยะ A คือระยะในแนวดิ่งจากจุด กึ่งกลางของ Sprocket ถึงจุดบนสุดของที่รองรับน้ำหนักด้านบน (Wear strip-Carry way) ระยะนี้มีผลกระทบกับ การเคลื่อนที่ของวัสดุ ณ.จุดเชื่อมต่อจาก conveyor ตัวหนึ่งไปสู่อีกตัวหนึ่งว่าจะส่งผ่าน Product ได้อย่างราบเรียบและสม่ำเสมอเพียงใด ระยะ B คือระยะในแนวราบจากจุดศูนย์กลางของเฟือง (sprocket) ไปยังจุดปลายของWear strip (carry way support) ระยะนี้เป็นตัวที่กำหนดที่มีผลกระทบกับสายพานว่าจะสามารถวิ่งได้ตรงก่อนเข้าเฟืองขับ (sprocket) โดยสายพานไม่งอเสียรูป (Buckle) เสียก่อน ผู้ผลิตบางรายแนะนำระยะ B เท่ากับหรือน้อยกว่า 1.5 เท่าของ Pitch สายพาน Model นั้นๆ ระยะ C คือระยะในแนวดิ่งจากระดับบน Wear strip (carry way support) ถึงระดับบนของลูกกลิ้ง (Snub) ระยะนี้มีความสำคัญคือจะเป็นตัวกำหนดว่าสายพานจะมีมุม โอบรอบ sprocket มากเท่าไหร่ ปกติแล้วสายพานควรมีมุมโอบรอบ sprocket ที่ 180 ถึง 210 องศาเพื่อให้สายพานและเฟือง (sprocket) ทำงานกันด้วยความราบเรียบสม่ำเสมอ ระยะ D คือระยะห่าง (Reserve Clearance) ระหว่างสายพาน กับโครงสร้างของคอนเวเยอร์ที่เผื่อไว้สำหรับการขยาย-หด ตัวของสายพานทั้งด้านกว้างและด้านยาว (หรือกรณี Alignment สายพานไม่ดี) ในทางปฏิบัติให้ใช้ระยะ 3-5 มม. อย่างไรก็ตามหากต้องการความละเอียด ระยะนี้ต้องคำนวณจากการเปลี่ยนแปลงอุณหภูมิของสายพานขณะที่ทำงานซึ่งสามารถขอตารางค่าสัมประสิทธิ์ของการขยายตัวของวัสดุชนิดต่างๆและสายพานได้จากผู้ขายสายพาน
D คือระยะห่าง (Reserve Clearance) ระหว่างสายพาน กับโครงสร้างของคอนเวเยอร์ ระยะ E คือระยะในแนวราบ จากจุดศูนย์กลางของเฟือง (sprocket) มายังคงจุดใดๆของโครงสร้างคอนเวเยอร์ ขอได้จากผู้ขายสายพานเมื่อเลือก Model ของสายพานได้แล้ว 5. Carry Ways หรือส่วนที่รับน้ำหนักบรรทุก (ด้านบน) Carry Ways หรือส่วนที่รับน้ำหนักบรรทุก (ด้านบน) ของ Conveyor สามารถวางได้หลายรูปแบบทั้งแบบตรงขนาน (ระยะห่างประมาณ 120-150 มม.) และวางแบบก้างปลา (ระยะห่างตามรูป)
Carry Ways หรือส่วนที่รับน้ำหนักบรรทุกรูปแบบตรงขนานสำหรับงานทั่วไป
Carry Ways แบบตรงก้างปลาเหมาะสำหรับงานหนัก
Carry Ways หรือส่วนที่รับน้ำหนักบรรทุกรูปแบบตรงก้างปลา
จุดประสงค์ของส่วนที่รับน้ำหนักบรรทุก (Carry Ways) นี้เพื่อจะลดแรงเสียดทานระหว่างสายพานและโครงสร้างโดยสามารถใช้วัสดุต่างๆดังนี้เช่น Ø ใช้แผ่นโลหะ(Metal), UHMW หรือ HDPE แบบเต็มแผ่น เป็น Slider Bed เต็มผิวหน้าตลอดทั้งผืน เหมาะสำหรับงานที่รับน้ำหนักมากๆ Ø ใช้ Wear strip ที่ใช้วัสดุประเภท UHMW หรือ HDPE ระยะห่างระหว่าง Wear strip (P) สามารถคำนวณได้ ขึ้นอยู่กับ Model ของสายพานที่เลือกใช้และน้ำหนักบรรทุกของวัสดุ (ระยะห่างแนะนำประมาณ 120-150 มม.) Wear strip ที่ใช้วัสดุประเภท UHMW หรือ HDPE
Ø Wear Strip มีหลายรูปหน้าตัด ดังนั้นการติดตั้งจึงทำได้ทั้ง ติด wear Strip โดยตรงลงบน โครงสร้างของ Conveyor หรือ ใช้ wear strip แบบสอดเข้าไปใน section ของเหล็กรูปพรรณได้โดยตรง ตัวอย่าง Wear Strip มีหลายรูปหน้าตัดหลายอย่าง
โดยเว้นช่องไว้ประมาณ 5 มม.ทุกๆระยะไม่เกิน 3 เมตร ในแนวเฉียงเพื่อให้สายพานวิ่งได้อย่างราบเรียบและเผื่อไว้สำหรับการขยายตัว-หดตัวเนื่องจากอุณหภูมิเปลี่ยนแปลง
เว้นช่องไว้ 5 มม.เผื่อการขยายตัว ตัดในแนวเฉียงเพื่อให้สายพานวิ่งได้อย่างราบเรียบ
Ø ไม่นิยมใช้ลูกกลิ้ง (roller) เป็น Carry Ways เนื่องจากไม่สามารถรองรับน้ำหนักสายพานได้เต็มหน้า ทำให้สายพานเด้ง(Bounce) ขึ้น-ลง ทำให้สายพานโก่ง (Sag) เกิด Chordal Effect สายพานกระตุก ฟันของเฟือง (Sprocket) กระโดด (Skip) หรือทำให้ Product ล้มได้ ในบางกรณีที่ความตึงของสายพานมีไม่มากพอที่จะทำให้สายพานยืดตรงได้ขณะเข้า Sprocket จะทำให้สายพานเกิดการแอ่นตัว(Buckle) ระหว่างจุดเชื่อมต่อของปลายของ Wear strip ถึง sprocket ทำให้เกิด Chordal Effect ปรากฏการณเช่นนี้สามารถแก้ไขได้โดยการยื่นWear strip เข้าไปอยู่ในช่องว่างระหว่าง Sprocket
ผู้ผลิตบางรายแนะนำระยะ B เท่ากับหรือน้อยกว่า 1.5 เท่าของ Pitch สายพาน Model นั้นๆเพื่อมาให้สายพานเกิดการแอ่นตัว (Buckle)
ยื่นWear strip เข้าไปอยู่ในช่องว่างระหว่าง Sprocket
ยื่นWear strip เข้าไปอยู่ในช่องว่างให้ใกล้กับจุดศูนย์กลาง ของ Sprocket มากที่สุดที่จะทำได้ไม่ทำให้สายพานเกิดการแอ่นตัว (Buckle) 6. คำแนะนำจำนวนแถว (Carry ways support) ส่วนที่รับน้ำหนักบรรทุก (ด้านบน) ความสัมพันธ์ระหว่าง Sprocket, หน้ากว้างของสายพาน
6. Return Ways หรือส่วนที่รับน้ำหนักสายพานด้านกลับ (ด้านล่าง) ส่วนรองรับสายพานด้านล่าง(Return Ways) ใช้ วัสดุและที่รองรับลักษณะเดียวกับส่วนที่รองรับที่อยู่ด้านบน (Carry ways) แต่สิ่งที่ต้องตระหนักและแตกต่างคือสายพานด้านล่างมีแนวโน้มที่จะแอ่นตัวได้สูงเนื่องจากน้ำหนักของตัวสายพานเอง ดังนั้นส่วนรองรับต้องที่มีจำนวนมากและใกล้กันเพียงพอที่จะไม่ทำให้สายพานแอ่นตัวมากเกินไป (ระยะห่างแนะนำไม่เกิน 200 มม.) หากต้องการที่จะใช้ Wear Strip รองรับสายพานเพียงสองด้าน ต้องเลือกความกว้างของสายพาน (W1) และความกว้างของ Wear strip (W2) ตามคำแนะนำของผู้ผลิต (ขึ้นอยู่กับรูปแบบ ความหนา Stiffness ของสายพาน) เพื่อไม่ให้สายพานแอ่นตัวมากเกินค่าที่กำหนดดังตัวอย่างตารางข้างล่าง
สายพานแอ่นตัวเนื่องจากน้ำหนักของตัวสายพานเอง
ค่า W1, W2ท่านสามารถขอรายละเอียดได้จากผู้ขายสายพายยี่ห้อที่ท่านซื้อได้ Ø Type หมายถึงรูปแบบหรือโมเดลของสายพาน เช่นโมเดล 100 -200- 300- 400 หรือ 500 เป็นต้น Ø W1 คือค่าความกว้างมากที่สุดของโครงสายพาน หน่วยเป็น มม. Ø W2 คือค่าความกว้างน้อยที่สุดของ wear strip หน่วยเป็น มม. 6.1Roller Support ส่วนรองรับสายพานด้านล่าง (Return Ways) เมื่อใช้ลูกกลิ้ง (Roller) เป็นส่วนรองรับสายพานด้านล่าง (Return Ways) ต้องใช้ขนาดเส้นผ่าศูนย์กลางของลูกกลิ้งให้เหมาะสมกับประเภท (Type) หรือ Model ของสายพานที่ใช้งานซึ่งแต่ละ Model จะมี Pitch ความหนา โครงสร้างและคุณสมบัติไม่เหมือนกันเพื่อป้องกันไม่ให้ท้องสายพานด้าน Return หักงอมากเกินไป
ข้อแนะนำเบื้องต้น การเลือกขนาดเส้นผ่าศูนย์กลางของลูกกลิ้งกับขนาด Pitch ของสายพาน (หน่วยเป็น มม.)
6.2 Return Ways แบบพิเศษ กรณีสายพานติดบั้ง (Cleat) หรือ Sidewall (ขอบกันตกด้านข้าง) สายพานประเภทนี้มีน้ำหนักมากดังนั้นจึงต้องการที่รองรับแข็งแรงและมีรูปแบบพิเศษ รองรับด้านล่างอาจจะใช้เป็นWear Strip หรือใช้เป็นWear Strip และลูกกลิ้ง (Roller) รองรับร่วมกันก็ได้
Wear Strip และลูกกลิ้ง (Roller) รองรับสายพานที่มีน้ำหนักมาก
6.3 Return wayแบบพิเศษสำหรับสายพานทำงานใต้น้ำ (Submerge Conveyor)
สายพานทำงานใต้น้ำ (Submerge Conveyor)
ซับเมิร์จคอนเวเยอร์(Submerge Conveyor)หรือคอนเวเยอร์ที่ทำงานอยู่ใต้น้ำเช่นใน Process การล้างผัก หรือสิ่งของต่างๆ วัสดุที่ทำสายพานต้องใช้เป็น POM เท่านั้นเพราะมีค่าความถ่วงจำเพาะมากกว่าน้ำ ขณะที่พลาสติกชนิดอื่น (PE/PE/NYLON) มีค่าความถ่วงจำเพาะน้อยกว่าน้ำจึงลอยน้ำ ในขณะที่คอนเวเยอร์ทำงานจมอยู่ในน้ำนี้จะมีแรงดันน้ำดันให้สายพานลอยตัวขึ้นด้านบน ดังนั้นในการออกแบบ Return Way จึงต้องติดตั้งล้อกดสายพาน(ดังรูป)หรือทำโครงสร้างกดสายพาน เพื่อบังคับให้สายพานจมน้ำอยู่ตลอดเวลา ขณะเดียวกันก็ต้องไม่ให้สายพานแอ่นตัวโดยเลือกรูปแบบการวางที่รองรับตามรูปข้างล่าง
Multi-Rail Supper zapping Wear Strip
การติดตั้ง Wear strip ทั้งบนและล่างเพื่อหนีบสายพานด้านกลับจะช่วยป้องกันไม่ให้สายพานลอยตัวเนื่องจากแรงดันของน้ำได้โดย Wear strip ด้านล่างจะเป็นตัวรองรับน้ำหนักของสายพานขณะที่ Wear strip ด้านบนจะกดสายพานไม่ให้สายพานลอยขึ้นดังนั้นโอกาสที่สายพานจะลอยตัวจึงไม่เกิดขึ้น
7. Wear Strip Under Low Temperature Environment การติดตั้ง Wear strip ในสถานที่มีอุณหภูมิเย็นมากๆ วัสดุที่ใช้ทำ Wear strip ไม่ว่าจะเป็น UHMWหรือ HDPE จะหดตัวและขยายตัวเมื่ออยู่ในสิ่งแวดล้อมที่มีอุณหภูมิเปลี่ยนแปลงจะทำให้สายพานเดินไม่เรียบดังรูป ลักษณะของ UHMWหรือ HDPE หดตัวและขยายตัวเมื่ออยู่ที่มีอุณหภูมิเปลี่ยนแปลง
เมื่ออุณหภูมิมีการเปลี่ยนแปลงสูงหรือต่ำมากกว่า 25 องศาเซลเซียสสลับกันไป-มา น้ำในอากาศจะกลั่นตัวเป็นน้ำแข็งเกาะอยู่บนผิวของ Wear strip ทำให้ Wear strip มีสภาพคล้ายรางที่มีน้ำแข็งเกาะอยู่ผิวบน ทำให้การหน้าที่รองรับของ Wear strip นั้นไม่มีประสิทธิภาพที่ดีพอ วิธีแก้ไขก็คือให้ใช้ที่รองรับที่มีพื้นที่ผิวสัมผัสน้อยน้อยแทน Wear Strip แบบมาตรฐานที่ใช้โดยทั่วไป ตัวอย่าง Wear strip ที่มีพื้นที่หน้าตัดน้อย หลายประเภทดังรูปข้างล่าง หรืออาจจะใช้เหล็กรูปพรรณที่มีหน้าตัดน้อยและพื้นผิวเรียบเรียบเป็นที่รองรับโดยตรงเลยก็ได้
ใช้ Wear strip ที่มีพื้นที่หน้าตัดน้อยในที่มีอุณหภูมิต่ำ
8.ไม่รู้จัก ในไลน์ ยังกล้าทัก ตัวเป็นๆน่ารัก รีบทักเลย ทีมงานพร้อมให้บริการด้วยหัวใจ สุดท้าย บริษัท คอนเวเยอร์ไกด์ จำกัด(Conveyor Guide Co.Ltd.) ขอขอบคุณท่านผู้อ่านทุกท่านที่ให้กำลังใจติดตามอ่านผลงานและสนับสนุนสินค้าของเรา เราสัญญาว่า จะนำเสนอเรื่องราวดีๆมีประโยชน์มาให้ท่านได้เรียนรู้ร่วมกันอย่างสม่ำเสมอ เราจะตอบสนองท่านอย่างมีประสิทธิภาพ ไม่หยุดนิ่ง เราไม่เคยทำงานลวกๆ หรือลดระดับการปฏิบัติงานตนเอง เราทราบวิธีและมีความสามารถ ที่จะสร้างสร้างความ เรียบง่ายบนซับซ้อนอยากใช้เราก็ติดต่อเราครับ ง่ายนิดเดียว สงสัยสิ่งใด ส่งรายละเอียดทั้งหมดมาทาง E-mail จะสะดวกดีมากครับ อยากรู้อะไรเพิ่มเติมอย่างเร่งด่วน โทรศัพท์มาสอบถามรายละเอียด ไม่รู้จักในไลน์ ยังกล้าทัก ตัวเป็นๆน่ารัก รีบทักเลย เรายินดีให้คำปรึกษาตลอดเวลา หรือต้องการให้เราไปอบรมหรือจัดสัมมนาให้หน่วยงานบำรุงรักษาในหน่อยงานของท่านก็ได้ (มีค่าบริการนะครับ) ไม่เพียงแต่เรื่องนี้เท่านั้นนะครับ เรื่องอะไรก็ได้ที่ท่านอยากรู้เกี่ยวกับสายพานลำเลียงก็ลองติดต่อเข้ามาได้อะไรที่แบ่งๆกันได้และไม่เปลืองทรัพยากรจนเกินไปก็ยินดีรับใช้ฟรีครับ เพราะเรามี Motto การทำงานคือ ‘’Together We Share ไปด้วยกัน...เผื่อแผ่กัน...แลกเปลี่ยน...เรียนรู้ ร่วมกัน’’ ครับ เราจะหาความรู้เกี่ยวกับอุปกรณ์ระบบลำเลียงมานำเสนออย่างสม่ำเสมอ “มีของเท่าไหร่ก็ปล่อยหมด ไม่มี กั๊ก ไม่มีดึง ไม่มีเม้ม” “ถึงแม้ว่าเราจะเดินช้า...แต่เราก็ไม่เคยหยุดเดิน” แล้วพบกันใหม่ครับขอบคุณที่ติดตาม
|